RECYCLE Ecological Recycle Rate Tests
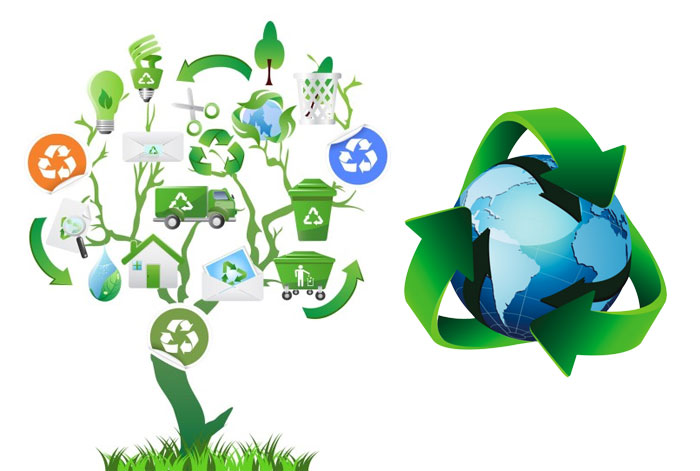
Natural resources are not endless, and unfortunately irresponsible and unconscious use of natural resources one day is at risk of depletion. On the other hand, consumption is increasing rapidly. For people and organizations who are aware of this fact, the concept of recycling has become increasingly important today. For example, recycling of used paper and cardboard and making it suitable for reuse as raw materials are very easy processes in today's production technologies.
Production processes that involve the conversion of various wastes such as paper, plastic, glass, aluminum, batteries, organic wastes and electronic wastes into secondary raw materials through physical or chemical processes are called recycling. In other words, recycling of the products that have reached the end of their useful life and lost their value to the economy is called recycling.
In order to maintain the assets of the enterprises and to be more profitable, less resources will be used with recycling processes, but less costs will be incurred. This is an important factor in gaining competitive power and increasing market share.
However, in spite of these advantages, some enterprises see investment and production in recycling technologies as an extra cost and stay away. As a matter of fact, production with recycled raw materials is a factor that reduces cost.
Recycling rate is a calculation process used to determine the percentage of directed waste. Some materials cannot be recycled because these materials are heavily contaminated or the center that can handle these materials cannot use certain recyclable materials. In a community with a percentage 30 deviation rate, only a percentage 10-15 recycling rate is acceptable.
Smarter product designs, supporting waste management plans and encouraging people to give up their old electronics have helped to increase the recycling of metals worldwide. The recycling rates of metals are, in many cases, much lower than their potential for re-use. Very little amount of metal in the vicinity of 20 studied has a recycling rate above 50. Furthermore, the recycling rate of more than 30 elements is less than 1 percent. Significant efforts are being made in many countries, but the recycling rate of many metals is extremely low.
Total and environmentally important recycling activities are the process of collecting and reprocessing materials that have reached the end of their life and which can be converted into new products. Thanks to recycling efforts, the amount of waste sent to landfills and incineration plants is reduced, natural resources such as trees, water and minerals are conserved, pollution is prevented and energy savings are achieved as the need for new raw material collection will be reduced.
There is a known recycling symbol on the materials whose raw material is recovered. This symbol is designed in the logo contest held in 1970. The three arrows in the symbol indicate reduction, reuse and recycling. The space in the middle of the symbol resembles a pine tree. This symbol symbolizes continuity with a limited being.
There are three basic steps to be taken in the recycling of waste: collection and processing, production and the purchase of products made from recycled materials.
Recycling studies involve a continuous cycle and tests and analyzes are carried out in advanced laboratories in this direction. There are countless domestic and foreign standards taken into consideration in these studies.
Our company also provides RECYCLE recycling rate test services within the scope of other testing services. Thanks to these services, enterprises are able to produce more efficient, high performance and quality products in a safe, fast and uninterrupted manner.
The recycling rate test services provided within the scope of other test services are only one of the services provided by our organization in this respect. Many other testing services are also available.